PASSTROUGH - PASSBOX - TRANSFER
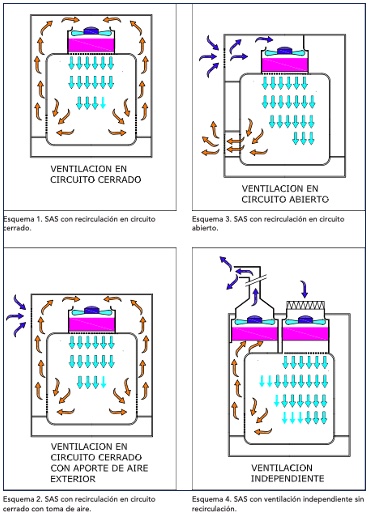
En este blog, discutiremos el artículo titulado "TRANSFERENCIA DE MATERIALES EN SALAS LIMPIAS: SAS Y ESCLUSAS" publicado en la revista FARMESPAÑA INDUSTRIALpor Miguel Ruiz / Miguel Ángel Rodríguez. Septiembre de 2017. El artículo aborda el objetivo principal de presentar las diferentes posibilidades de transferencia de materiales en la industria farmacéutica con la utilización de PASS-TROUGH / PASSBOX / TRANSFER / PASAMATERIALES en especial en Salas Limpias o Áreas Limpias y así garantizar un entorno controlado y llevar a cabo operaciones y procesos sensibles.
La continua interacción con el exterior o con otras partes de menor Grado de la propia Zona Limpia es una de las principales fuentes de contaminación y uno de los puntos clave a tener en cuenta en el diseño de una Zona Limpia.
Normativa aplicable
El sistema comúnmente aceptado y ampliamente conocido para la transferencia de materiales y personas es el sistema de esclusas. En el Glosario de las GMP euro- peas se define esclusa como:
"Espacio cerrado con 2 o más puertas, interpuesto entre 2 o más salas, por ejemplo de distinto nivel de limpieza, con el fin de controlar la circulación de aire entre dichas salas cuando se pasa a las mismas. Las esclusas se diseñan para su uso por personas o por objetos"
EU GMP solo profundiza algo más en las características y usos de las esclusas en el Anexo 1 "Fabricación de Medicamentos Estériles", donde se dan unos conceptos muy generales que básicamente se refieren a la necesidad de asegurar que las puertas de la esclusa no pueden abrirse de forma simultánea. No hay referencias explicitas a la presión y clasificación que debe tener la esclusa, por lo que implícitamente se asume que la esclusa debe seguir el precepto general del escalonamiento de presiones "desde la zona más limpia hacia la zona menos limpia". No hay más referencias en EU GMP con respecto a otras características que debe cumplir una esclusa.
Para esclusas de personal hay unas referencias más concretas en el punto 51 del Anexo 1, donde se indica la necesidad de una sucesión de esclusas para "proporcionar una separación física de las diferentes fases de cambio de vestimenta...". En este mismo punto se indica una de las características más concretas aplicables a las esclusas de personal: "La fase final del vestuario deberá tener, en situación de reposo, el mismo grado que la zona a la que conduzca"
La normativa americana USA cGMP utiliza definiciones generales muy parecidas; en "Guidance for Industry Sterile Drug Products Produced by Aseptic Processing" se dan unos conceptos muy generales que no van más allá de la necesidad de prevenir la apertura simultanea de las puertas y establecer un régimen de escalonamiento de presiones con valores entre 10 y 15Pa, que debe ser de al menos 12,5Pa cuando la esclusa comunica la Zona Estéril con una zona No Clasificada.
EU GMP y USA cGMP son las guías principales en todo lo relacionado con zonas limpias de producción farmacéutica; sin embargo fueron editadas hace bastante tiempo (la revisión del Anexo 1 es de 2009 y Guidance for Industry de estériles es de 2004) por lo que la practica general está superando los conceptos expresados en estas normas.
Es interesante ver como otras normativas, que generalmente coincidían literalmente con EU GMP están definiendo conceptos más avanzados. Por ejemplo el Anexo 6 de la OMS para estériles, en su edición de 2002 coincidía literalmente con el Anexo 1 de EUGMP de 2002 y de 2009 en lo relativo a las esclusas de personas y materiales; sin embargo la edición de 2011 introduce un cambio sustancial, se añade un párrafo en el que se indica que no debe haber un salto de más de un Grado entre las esclusas consecutivas de vestuarios, así́ un pasillo D debería comunicar una esclusa C que a su vez debería comunicar con un vestuario B que finalmente desembocaría en una sala B . Este es un concepto que en general se apli- ca en todos los vestuarios de Zonas Limpias, sin embargo en ninguna normativa anterior había sido recogido explícitamente.
En la misma línea el documento de la OMS "Environmental Monitoring of Clean Rooms in Vaccine Manufacturing Facilities" de 2012 establece que el grado de un air- lock debe corresponder al del área anexa de mayor grado.
También es interesante ver como algunas normativas nacionales que se apoyan generalmente en OMS GMP y EU GMP evolucionan incluso por delante de estas. Por ejemplo el borrador en fase de aprobación de las GMP Argentinas, en su Anexo 9 fabricación de Medicamentos Estériles propone que:
"La fase final del vestuario o de la esclusa de materiales debe tener, en situación de reposo, el mismo grado que la zona a la que conduzcan"
Esta es la primera normativa GMP que indica explícitamente que una esclusa de materiales deba tener el mismo grado que la zona a la que conduce. En general era comúnmente aceptado que una esclusa de materiales tuviese un Grado inferior a la zona a la que conduce. El típico esquema de entradas/salidas a una zona de producción grado B desde una zona exterior grado D solía ser mediante un vestuario de dos pasos C y B y una esclusa de materiales C.
La diferencia fundamental entre esclusas de vestuario y esclusas de materiales, además del uso a la que están dedicadas, es que la esclusa de personal puede estar compuesta por varios pasos sucesivos, ya que el personal se mueve por sí mismo dese un paso al siguiente; sin embargo la esclusa de materiales está compuesta por un solo paso porque el material tiene que ser movido por personas y estas no deben cruzar pasos consecutivos que impliquen cambio de Grado sin hacer un cambio de vestuario. El proceso general de transferencia de material en una esclusa implica a dos personas situadas a cada extremo de la esclusa, una persona introduce el material desde el lado "sucio" entrando en la esclusa lo menos posible y otra persona extrae el material desde el lado "limpio" también entrando en la esclusa lo menos posible; obviamente debido al enclavamiento de puertas ambas personas no coinciden dentro de la esclusa en el mismo momento.
La transferencia de materiales hacia o desde Zonas Limpias se realiza básicamente mediante esclusas o SAS, considerando una esclusa como una sala interpuesta entre dos zonas de distinta clasificación y a un SAS (Safety Access System) como una "caja" de tamaño más reducido, interpuesta en la pared de separación entre dos zonas de distinta clasificación. En la normativa y bibliografía GMP se emplean otros términos sinónimos de SAS como Pass Thru, Pass Box o Pasamateriales. Puede considerarse también como un caso especial de sistemas de transferencia los hornos y autoclaves de doble puerta y los túneles de esterilización.
La filosofía actual de las GMP tiende a evitar la indicación de soluciones técnicas concretas y basar el diseño y la adopción de medidas técnicas tras la realización de un análisis de riesgos. En este sentido esclusas y SAS de materiales pueden dotarse de una serie de medidas técnicas encaminadas a cumplir los requerimientos del análisis de riesgos.
Doble puerta
El primer concepto de protección en un SAS o esclusa es la existencia de doble puerta. Esta característica mitiga el contacto entre la Zona No Controlada y la Zona Limpia interponiendo en todo momento una puerta cerrada entre ambos espacios. La condición necesaria es que ambas puertas no puedan ser abiertas al mismo tiempo, esto se consigue con la instalación de semáforos indicadores, alarmas acústicas y/o enclavamientos mecánicos o magnéticos en las puertas. Así el tipo más simple de esclusa viene representado por un sistema de doble puerta con enclavamiento e indicación del estado de las puertas. En el caso de esclusas o SAS con tres o más puertas, la apertura de una sola de ellas debe bloquear a las demás.
Radiación germicida UV
En el caso de las esclusas, entendidas como salas integradas en el layout, estás suelen estar ventiladas y clasificadas por el sistema general de HVAC, por lo que su interior se mantiene en unas condiciones controladas.
Sin embargo los SAS de paso, entendidos como simples cajas de doble puerta, no tienen ningún tipo de control del aire de su interior. Dado su pequeño volumen es difícil que durante su operación tengan capacidad para incrementar de forma sensible el nivel de partículas de la zona Limpia; seguramente las partículas ingresadas en la zona a través del volumen del SAS sean bastante menos que las generadas en el interior de la Zona Limpia por los operarios y los sistemas de producción. Sin embargo la contaminación biológica que puede crecer en la cámara del SAS cuando este permanece inactivo ya no ser despreciable y podría llegar a inducir un aumento de la contaminación viable en la Sala Limpia por encima de los límites admisibles.
La adición de una lámpara germicida UV que se mantiene activa mientras el SAS está vacío, reduce la carga biológica de su interior y por tanto el número de partículas viables que pueden pasar a la zona limpia durante la operación de transferencia.
La radiación germicida UV también puede utilizarse para reducir la carga biológica depositada en la superficie del material que se está transfiriendo; pero en estos casos una sola lámpara no es suficiente y se debe asegurar que la radiación transmitida tiene la potencia suficiente y alcanza a toda la superficie del material. Se hace necesario colocar lámparas UV en todo el perímetro interior del SAS, paredes, techo y fondo e instalar una rejilla a media altura para depositar el material y permitir que reciba radiación UV también en su parte inferior. El SAS debe completarse con una temporización que mantenga ambas puertas enclavadas durante el tiempo de radiación validado, así como un enclavamiento de protección que desconecte automáticamente la luz UV ante la apertura de puertas. Debido al desgaste de las lámparas UV es conveniente un contador horario para controlar el tiempo de funcionamiento de estas lámparas y permitir su cambio antes del fin de su vida útil.
Sistema de ventilación
Cuando el nivel de partículas introducido en la Sala Limpia durante la operación de transferencia no es admisible, o cuando se quiere seguir la recomendación de que "el Grado del SAS o esclusa sea el mismo que la sala a la que accede", el SAS o esclusa debe estar provisto de un sistema de barrido interior con aire ultra filtrado.
En el caso de las grandes esclusas el sistema de HVAC ya es capaz de mantener un cierto Grado de clasificación interior, sin embargo la apertura de la puerta del lado "sucio" afecta a la clasificación de la esclusa por lo que es conveniente un sistema que asegure que el interior de la esclusa ha recuperado el Grado de clasificación especificado antes de proceder a la apertura de la puerta del lado "limpio". Este efecto pue- de conseguirse completando el sistema de enclavamiento con una temporización que retarda la apertura de la puerta hasta que la esclusa recupera el Grado de clasificación. Un test de recuperación realizado durante la etapa de validación dará́ una indicación de cuál debe ser el tiempo de retardo.
El tiempo de retardo puede reducirse significativamente instalando un sistema de recirculación HEPA como ventilación de refuerzo; este sistema entra en marcha una vez que se cierra la puerta del lado "sucio", complementando la acción del sistema de HVAC. Una vez abierta la puerta del lado "Limpio" y descargada la esclusa, el sistema de recirculación se para, siendo el sistema de HVAC el encargado de mantener las condiciones de presión y ventilación de la esclusa.
En el caso de los SAS un sistema de ventilación HEPA, funcionando durante un tiempo determinado en el proceso de transferencia, permite asegurar que la cá- mara del SAS alcanza el mismo Grado que la zona limpia antes de la apertura de la puerta. Los SAS HEPA pueden tener varios tipos de sistemas de ventilación
Recirculación HEPA en circuito cerrado
Es el más simple, consiste en un ventilador y un filtro HEPA actuando en circuito cerrado sobre la cámara; este sistema consigue clasificar la cámara en el Grado requerido, pero al ser circuito cerrado no puede actuar sobre la sobre presión interior de la cámara para mantener un escalón de presiones sobre la Sala "Sucia" y la Sala "Limpia". En cualquier caso las puertas de un SAS son de alta hermeticidad por lo que no sería tan necesario un sistema de escalonamiento de presiones
Recirculación HEPA en circuito abierto
El sistema de ventilación del SAS toma aire de una de las salas (normalmente la sala "sucia") lo filtra a través de HEPA y lo devuelve a la sala "sucia" a través de una rejilla inferior; este sistema consigue el Grado de limpieza en la cámara y mantiene el SAS en una presión superior a la sala "sucia", pero hay una comunicación abierta entre la cámara del SAS y la sala "sucia" a través de la rejilla de salida de aire. Esto hace que cuando se abre la puerta de zona "limpia" haya una comunicación directa entre zona "limpia" y zona "sucia" a través de la cámara y la rejilla de salida de aire, aunque la puerta de zona "sucia" este cerrada y enclavada.
Con el sistema de ventilación en funcionamiento continuo el flujo de aire limpio evitaría el ingreso de contaminación desde zona "sucia" hacia zona "limpia", pero la parada del sistema de ventilación significaría una posibilidad de contaminación.
Recirculación en circuito cerrado con toma de aire
En algunos casos el sistema de recirculación se complementa con una pequeña toma de aire de la zona "sucia" antes de filtro HEPA que ayuda a sobre presionar la cámara del SAS. Este es un caso similar al anterior, mientras el sistema está en funcionamiento el régimen de presiones y el flujo de aire evita la contaminación des- de zona "sucia" a zona "limpia", pero la parada del sistema de ventilación implica una posibilidad de contaminación.
Ventilación independiente sin recirculación
En este caso el sistema de ventilación es totalmente independiente de las salas, toma el aire de una zona técnica a través de un pre filtro y lo introduce en la cámara mediante un ventilador y un filtro HEPA. El aire se extrae de la cámara mediante otro filtro HEPA y otro ventilador y se expulsa al exterior. Actuado sobre la velocidad de los ventiladores puede balancearse la presión interior de la cámara para mantenerla en el escalonamiento preestablecido. En pura teoría el filtro HEPA de extracción no sería necesario, pero es muy recomendable para evitar que durante la parada de ventiladores la contaminación exterior pueda entrar a la cámara. El sistema de ventilación independiente permite que cuando el SAS no está en uso los ventiladores estén parados y solo se ponen en marcha durante las operaciones de transferencia. También permite que durante la apertura de la puerta "sucia" el ventilador de extracción este parado de forma que todo el aire limpio impulsado al interior de la cámara salga hacia la zona "sucia" evitando el ingreso de aire "sucio" en la cámara. De la misma forma, durante la apertura de la puerta "limpia" el ventilador de extracción se mantiene en marcha de forma que el aire de la cámara no sale hacia la zona "limpia"
En cualquier caso, sea cual sea el modelo de ventilación, este tipo de SAS necesita de una automatización mediante PLC para gobernar la interacción entre ventiladores, enclavamientos de puertas, temporizaciones etc. incluso debería permitir discriminar entre un ciclo de entrada hacia zona "limpia" y un ciclo de salida hacia zona "sucia" .
SAS y esclusas de descontaminación
En los accesos a zonas estériles no solo la concentración de partículas es importante, también lo es la contaminación biológica que puede introducirse en la operación de transferencia. Los límites de partículas viables en zonas de grado A y B son tan estrictos que cualquier transferencia de materiales que no hayan sido debidamente descontaminados pone en riesgo los limites microbiológicos. En este sentido el
Anexo 1 (Estériles) de las GMP claramente especifica en su punto 81:
"Los componentes, envases, equipo y demás artículos necesarios en la zona limpia, cuando se esté́ realizando un trabajo aséptico deberán esterilizarse e introducirse en la zona mediante equipos de esterilización de doble puerta situados en la pared, o mediante un procedimiento que proporcione el mismo resultado de no introducir contaminantes".
Por tanto los materiales que no pueden ser descontaminados por calor deberán ser introducidos a través de SAS o esclusas que incorpore un sistema de descontaminación por medio de biocidas: peróxido de hidrogeno en vía gas (VHP) nebulización de peróxido, peracético, glutaraldehído u otros desinfectantes por vía aérea.
Este tipo de SAS o esclusa requiere de un sistema de ventilación independiente en ciclo abierto, ya que la recirculación en ciclo cerrado no facilita la ventilación para la eliminación del biocida una vez completada la desinfección y los sistemas de ciclo cerrado con toma de aire permitirían que el biocida nebulizado saliera a las zonas ocupadas. En el caso de esclusas, estas no deben estar conectadas al sistema de HVAC para evitar que el biocida pase al resto de salas a través de los conductos de aire. Tanto para esclusas como para SAS el sistema más adecuado es la ventilación independiente en circuito abierto con impulsión HEPA y extracción HEPA.
Otro requisito imprescindible en estos SAS y esclusas es la existencia de puertas totalmente estancas para evitar la salida del biocida a zonas ocupadas, tanto en zona "limpia" como en zona "sucia". En el caso de los SAS la estanqueidad de puertas puede conseguirse mediante juntas continuas de prisión (juntas estáticas) o mediante juntas hinchables por aire comprimido (juntas dinámicas) En el caso de las esclusas lo más adecuado son las juntas dinámicas de aire comprimido ya que la junta estática requiere un escalón en el umbral de la puerta para dar continuidad al cierre a presión (lo que se suele denominar puerta tipo "submarino"); este escalón obliga a la instalación de rampas abatibles para manejar el equipo pesado sobre ruedas (carros, reactores...) . En el caso de las puertas de junta hinchable no es necesario escalón porque el marco contra el que cierra la junta hinchable que- da embebido en el suelo, permitiendo el paso de material pesado sobre ruedas.
Los ciclos típicos de un SAS de descontaminación son:
Pre-tratamiento
En función del tipo de biocida que se va a inyectar puede ser necesario un acondicionamiento previo de la cámara, para alcanzar unas condiciones de temperatura y humedad que aseguren el óptimo funcionamiento del biocida.
Inyección
En esta etapa se produce la inyección del biocida, durante un tiempo determinado hasta conseguir la concentración especificada.
Contacto
Una vez terminada la inyección se mantiene la cámara con la concentración de biocida en el ambiente durante un tiempo especificado.
Ventilación
En esta etapa se ventila la cámara mediante la inyección y extracción de aire ultra filtrado hasta reducir la concentración de biocida por debajo de los límites de seguridad, para la protección del personal que va a descargar el SAS o esclusa (por ejemplo en el caso del peróxido de hidrogeno este límite es inferior a 1ppm)
En el caso de los SAS de descontaminación un sistema de control mediante PLC es imprescindible, tanto para el desarrollo y temporización de las fases del ciclo como para establecer una serie de protecciones que eviten un mal funcionamiento, como inicio de inyección con una puerta abierta, apertura de puertas durante alguna de las etapas, gestión de abortos de ciclo y para- das de emergencia etc...
El PLC también gestiona el uso del SAS como esclusa de ventilación cuando el tránsito de materiales es de zona "limpia" hacia zona "sucia" y no se requiere un ciclo de descontaminación sino un ciclo de ventilación previo a la apertura de puerta de zona "limpia".
La gestión de abortos de ciclo también es importante ya que un ciclo abortado después de que se haya producido la inyección de biocida requiere obligatoriamente una etapa de aireación completa, antes de permitir la apertura de la puerta de zona "sucia". Y en ningún caso puede permitir la apertura de la puerta de zona "limpia" ya que la descontaminación no ha sido completada.
Arquitectura de SAS y esclusas
Los materiales y características técnicas de los SAS y esclusas deben cumplir con las directrices GMP en el sentido de ser materiales inertes, que no desprendan partículas y que sean fácilmente limpiables, evitando oquedades, rincones y ranuras de difícil acceso.
Los SAS suelen estar construidos en acero inoxidable, aunque algunos SAS de paso se construyen como pequeñas cajas utilizando los mismos materiales de las salas blancas y los mismos tipos de puertas.
En todo caso el criterio que debe seguirse en un SAS es el de facilidad de limpieza: todas las partes del SAS en contacto con el producto con las salas deben ser fácilmente limpiables. En este sentido hay que tener en cuenta que a veces las soluciones más "estéticas" no tienen por qué ser las más "limpias".
Cualificación
Por último y no menos importante, es necesario que todo SAS o esclusa tenga una cualificación completa, empezando por una DQ que asegure que las soluciones adoptadas son las más adecuadas para el fin perseguido, una IQ que asegure la calidad de la instalación y unas OQ y PQ que permitan validar las prestaciones del SAS y fijar con suficiente nivel de confianza las temporizaciones de los ciclos así como los enclavamientos y seguridades implementados.